Membrane Technologies
Membrane based processes are the future of green industrial fluids separation with low operational cost and high-quality end products.
- Generally, membrane-based processes are divided into two types, Pressure driven membrane sepration processes such conventional membrane filtration systems like Microfiltration (MF), Ultrafiltration (UF), Nanofiltration (NF) and Reverse Osmosis (RO) systems. While the other type is thermally driven membrane separation processes such as membrane distillation (MD), pervaporation (PV) and vapour permeation (VP) solutions.
- Thermally driven membrane-based solutions are great alternatives to conventional thermal distillation, as they can achieve higher separation efficiency at lower temperatures while thermal distillation fails to achieve the desired separation efficiency in many application due to azeotropes.
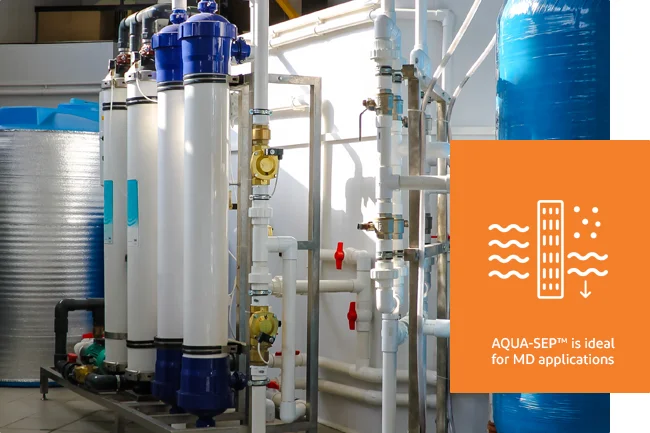
Membranes Distillation (MD)
Membrane Distillation (MD) is considered as one of major emerging techniques for separation of ono-volatile solutes from water. MD is a thermally driven membrane based separation process, in which porous hydrophobic membrane is used for separation. MD has the ability to use low grade and inexpensive heat sources, smaller plant footprint, and lower capital costs than conventional distillation processes.
In MD, the membrane is not involved in the transport phenomena on the basis of its selective properties. The microporous polymeric material acts as physical barrier between two phases and sustains the interfaces where heat and matter are simultaneously exchanged.
The large contact angle of water with the hydrophobic membrane prevents liquid water from penetrating the pores, and water vapor is transported across the membrane in response to a change in partial pressure due to a thermal gradient.
Among MD processes, variations exist as to the method by which the vapor is recovered once it has migrated through the membrane. MD systems can be configured in a number of ways, depending on the nature of the cold side of the membrane. In direct contact MD (DCMD) the membrane is in direct contact with the feed on one side and permeate on the other. While in air gap MD (AGMD) an air gap is interposed between the membrane and a cold condensation surface are perhaps most appropriate for desalination applications. Other configurations, such as vacuum MD (VMD) and sweeping gas MD (SGMD) methods, are typically used for stripping of volatile organics or dissolved gases.
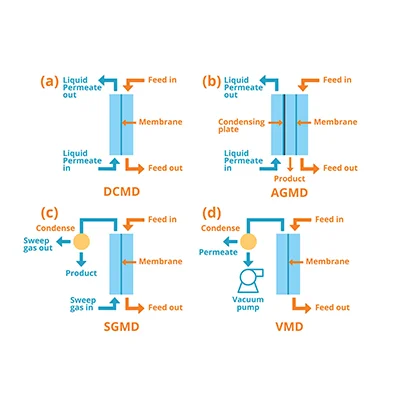
The major requirement of MD membranes is that they should not be wetted by the process liquids. To avoid liquid invasion of the pores, highly hydrophobic membranes with an appropriate pore size are used. The liquid surface tension also affects wetting. Organic solutes present in an aqueous solution reduce the surface tension to the point where spontaneous membrane wetting may occur. At this point, the surface tension is called the critical surface tension at which MD is no longer possible. Therefore, aqueous solutions containing inorganic solutes or low concentrations of volatile organic compounds can be treated while solutions with surface active components cannot.
The second major consideration in membrane selection for this process is pore size and porosity. High porosities are of special interest since the area available for evaporation is directly related to flux. However, high porosities are usually associated with large pore sizes, which are undesirable as they increase the risk of membrane wetting.
MD vs Distillation
The potential advantages of MD, in comparison with conventional separation processes, are found primarily in the lower working temperature and pressure, and thus the lower energy costs and less stringent mechanical properties. In contrast to distillation, supply solutions can be separated at a temperature well below the boiling point and under atmospheric pressure. Typical supply temperatures around 30-60°C permit re-use of residual heat flows, and the use of alternative energy sources such as sun, wind and geothermic.
In comparison with traditional distillation, MD possesses typical basic advantages of membrane separation, namely simple up-scaling, simple operations, possibility for high membrane surface/volume ratios, possibility to treat flows with heat-sensitive components and/or a high suspended particle-content at atmospheric pressure and a temperature below the boiling point of the supply.
MD vs. RO
Since permeate flux in a RO process is controlled by the osmotic pressure of treated water, a high-water recovery cannot be achieved with an elevated salinity. While in MD process, the osmotic pressure is not a limiting factor, allows for a significant increase in water recovery. In addition to that, MD is less susceptible to flux limitations caused by concentration polarisation. Theoretically, MD offers 100% rejection for non-volatile dissolved substances with no limit on the feed concentration.
The main disadvantage of MD compared to RO are the relatively low permeate flux, flux reductions caused by concentration polarisation, membrane pollution, water loss due to conduction through the polymeric membrane and/or pore wetting, and the high thermal energy consumption, for which the economic costs are determined by the MD configuration and the specific application.
MD with RO
There are two ways in which MD and RO can be integrated. The first is by using the RO brine as feed to the MD, or RO permeate as feed to the MD.
Using RO brine as a feed to MD has a great potential for MD utilization. This directly addresses the upper concentration limit of RO at around 70,000 mg/L, as MD is far less influenced by salt concentration. Typically, the need for an RO-MD process to increase water recovery is for inland applications where disposal of the brine is an issue. Testing of MD on RO groundwater concentrates revealed that the concept is indeed viable, but suffers from practical issues such as scaling on MD membranes. Membrane scaling led to flux declines, but flux was easily restored using an acid clean. Scaling was found to be effectively managed by cleaning or the addition of scale inhibitor.
MD can be used for the production of distilled water and for concentrating aqueous solutions. De-salting sea water and the production of clean water from brackish water are the most common MD applications because non-volatile ionic particles are almost completely retained.
MD is used for the water purification in the pharmaceutical, chemical and textile industries, for the concentration of fruit juices and milk processing, in bio-medical applications like the removal of water from blood, in the concentration of cooling liquids (glycols), non-volatile acids and oil-in-water emulsions and applications where high temperature processing causes thermal degradation of the process flow. MD can be used for the treatment of textile industry wastewater that is contaminated with dyes.
Petro Sep has developed AQUA-SEP™ that is based on the VMD principle for separation.
Vacuum Membrane Distillation (VMD)
VMD is a significant variant of the MD process. VMD is potentially the most efficient MD configuration, since there are no heat losses through the membrane and mass transfer resistance is reduced to the minimum. VMD is considered as a better option than DCMD for the desalination of high feed salt concentrations since membrane fouling in VMD, is usually low and can be controlled through chemical or water wash. VMD main advantage is the relatively low-conductive heat loss compared to DCMD.
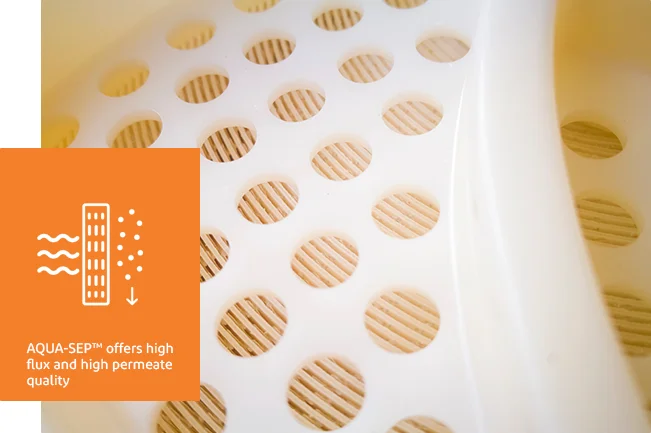
In VMD the aqueous feed is brought into contact with one side of a hydrophobic, microporous membrane. While the other side of the membrane is kept under vacuum. The hydrophobic nature of the membrane prevents the penetration of the aqueous solution into the pores, resulting in a vapor–liquid interface at each pore entrance. The driving force of the vapor molecules to pass through the pores is the vapor pressure difference between both ends of the membrane pore due to the applied vacuum pressure on the permeate side of the membrane. This created pressure difference between the two sides of the membrane enhances the total mass transfer as compared to DCMD. Then vapors passing through the membrane condensed in an external condenser.
- Porous Membranes
- Hydrophobic Membranes
- Driving force is the differential pressure between the aqueous feed stream the vapor stream under vacuum, resulting in high flux.
For the scale up of VMD system, MVR integration would be of great importance to optimize the required heat for the process. The feed solution is preheated by auxiliary heat source and enters the shell-side of the VMD hollow fiber membrane module by using a circulating pump. The bulk solution in VMD module is in contact with the hot side of the hydrophobic microporous membrane, while the vacuum is applied on the permeate side of the membrane by a vacuum pump. The water molecules reach the membrane surface through the thermal boundary layer and absorb the heat to evaporate.
The evaporation temperature for a certain concentration of feed solution at the membrane surface may be higher than that of the saturation temperature of pure water corresponding to the vapor partial pressure at the hot side membrane surface.
Condensation of vapor that passes through the membrane is performed outside the membrane section. The vapors flow out of the module to the compressor where their temperature and pressure increase due to the compression process. While brine solution temperature decreases due to evaporation. After outlet brine stream exist the membrane, it enters into condenser to condense the vapour comes the from compressors discharge. The condensate is collected permeate tank that is connected to vacuum pump. While the concentrated brine solution returns to the feed tank for further circulation and concentration.
However, the major problem with VMD process is chance for pore wetting due to higher pore wetting. The VMD mode of operation is considered to have two advantages, in comparison to other MD variants:
- relatively low-conductive heat loss and
- reduced resistance to mass transfer.
Despite the above potential benefits, the development of VMD for large-scale applications appears to be lagging behind other MD versions, notably DCMD.
A study concluded that VMD is the most proficient among the three MD configurations of VMD, DCMD and SGMD by exhibiting the highest flux and extent of desalination with the lowest freshwater conductivity.
VMD can be applied to the treatment of aqueous streams for recovering purified water or for extracting specific volatile compounds. Some examples of VMD applications could be seawater desalination, treatment of the reject stream of reverse osmosis systems, treatment of dye solutions, concentration of sugar solutions, arsenic removal from water, waste water treatment by removal of heavy metals, mine waste water treatment, and oily waste water treatment.
Petro Sep has developed AQUA-SEP™ that is based on the VMD principle for separation.
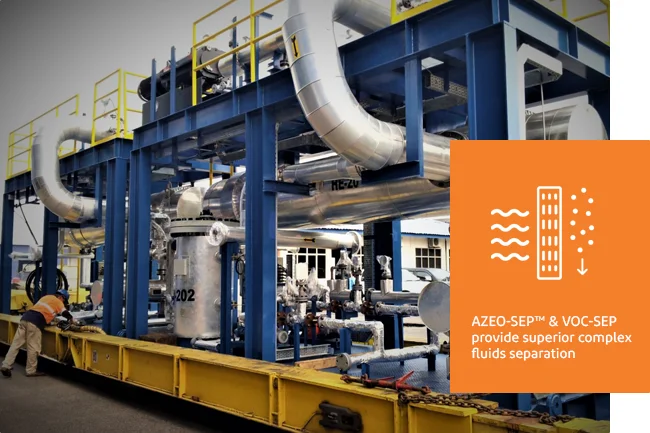
Pervaporation (PV)
In PV, the mirror component in the feed stream is separated from the bulk by preferential transportation through a semi-permeable barrier by its partial vaporization. Separation of azeotropic, close boiling, isomeric or heat sensitive liquid mixtures, recovery of volatile organic compounds (VOC), organic/ organic separation, recovery of trace concentrations of organic pollutants from industrial effluents and solvent dehydration are the major areas of application of PV process.
The main interest of PV is that the separation is not based on the thermodynamic equilibrium between the vapor and liquid phase, as occurs in distillation. This means that the concentration of the permeate is not defined by the vapor-liquid equilibrium but by the permeability of the compounds through the membrane, which depends on their solubility and diffusion rate in the membrane.
The driving force for the separation is the difference in the vapor pressures of the components at the two sides of the membrane which is continuously maintained by the applied vacuum on the permeate side of the membrane. The selectivity of the separation is given by different transport rates of the molecules through the membrane as a result of different solubilities and diffusivities of the components.
In the PV process, the feed solution is kept at a specific temperature and pressure that ensure a liquid phase during the operation (i.e., temperature lower than the boiling point and pressure higher than the bubble point of the feed). A dense non-porous membrane is required to perform the selective separation process of a specific compound from the mixture and thus control the efficiency of PV process. The components that permeate through a non-porous perm-selective membrane vaporize somewhere inside the membrane until reaching the other side, that is, the permeate side. The permeate side is kept normally under vacuum so that a large driving force is ensured. The components that have permeated (the “permeate”) are condensed and collected again in a liquid phase. The liquid stream that did not permeate through the membrane is called “the retentate” and is concentrated in the less permeant species.
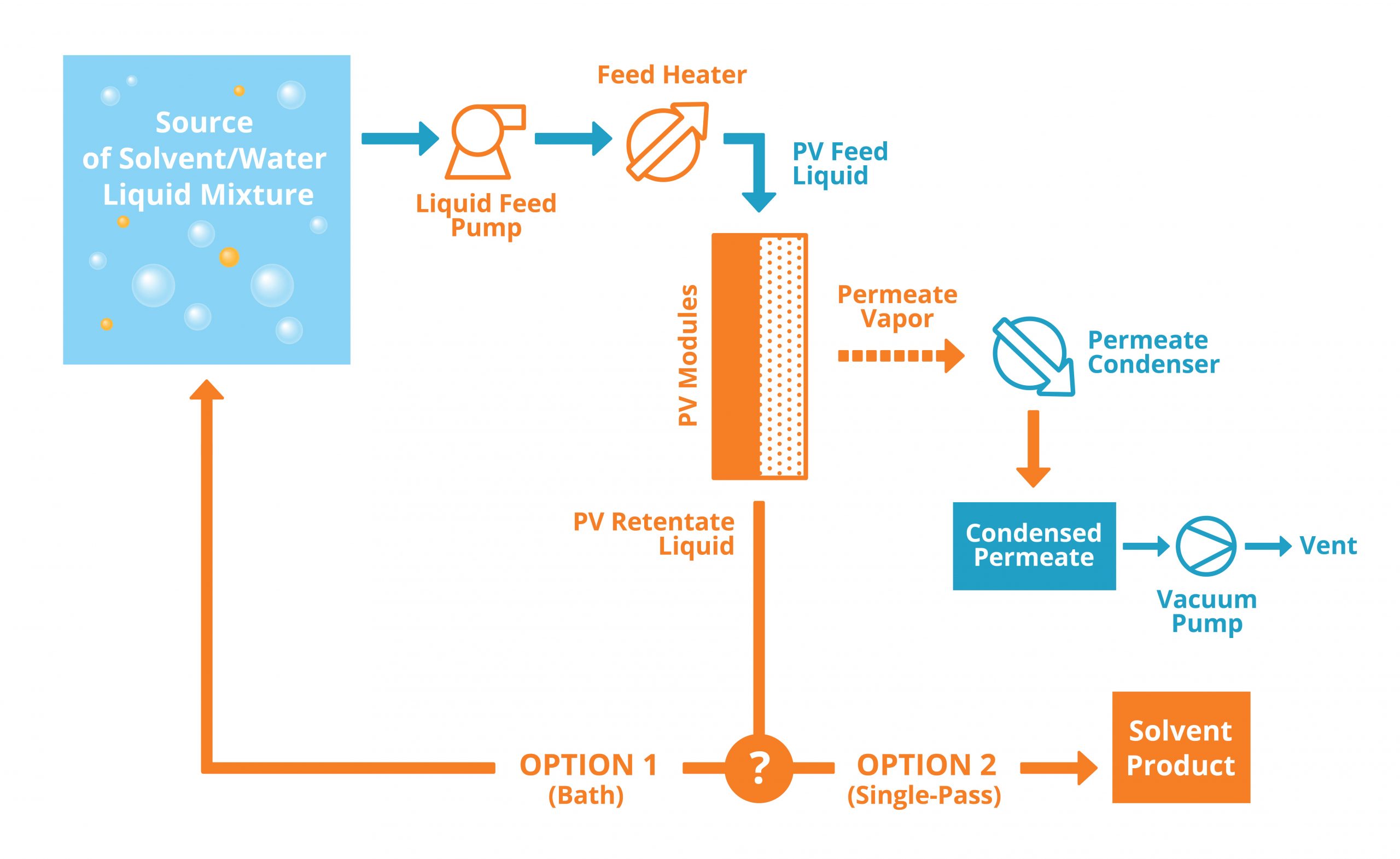
PV Membrane Types
Hydrophilic, hydrophobic, and Organophilic types of membranes can be used in PV based on feed type:
- Hydrophilic membranes are used to separate water from organic solvents. These membranes basically remove water present in small concentrations in azeotropic mixtures. Applications of such membranes include dehydration of azeotropic mixtures like ethanol/water, isopropanol/water and dehydration of dimethylformamide (DMF), and acetone containing water content less than 10%.
- Hydrophobic membranes are used for removal of organics (volatile organic compounds) that are present in very low concentrations in aqueous solutions.
- Organophilic membranes can extract organic compounds from aqueous solutions and separate binary or multicomponent organic mixtures such as those comprising of polar-nonpolar, isomeric, and aromatic-alicyclic compounds.
For the selection of a suitable membrane some parameters should be considered. Such as degree of hydrophilicity, chemical and thermal stability and the selectivity and permeability of the target component. Depending upon the feed composition, the desired permeate purity, the PV application can be classified into:
- Solvent dehydration: Solvent dehydration refers to the removal of the trace amount of water present in various organic solvents by use of a hydrophilic PV membrane. PV is extensively used for dehydration of alcohols like ethanol, isopropanol, t-butanol etc. which possess strong binding affinity towards water resulting in the formation of an azeotropic mixture at a certain composition. It is very difficult to remove that trace amount of water from these azeotropic mixtures by conventional processes like distillation or solvent extraction.
- Organophilic Separation: Recovery of trace organic compounds from aqueous industrial streams for environmental safety, isolation of alcohols in bioethanol production, organic solvent recovery from gas scrubbing wash water, and aroma recovery from plant extracts are challenging areas of research. PV allows the target organic compounds to preferentially pass through. The membranes are mostly hydrophobic and non-polar in nature to restrict the permeation of water. The limitation of hydrophobic membrane is the lower selectivity. The hydrophobic nature restricts the permeation of water and allows organics to permeate, but due to low molecular size, some water molecules still manage to diffuse through the membrane, because of which, selectivity reduces.
- Organic/Organic Separation: Recovery of certain value-added organic compounds from industrial process streams carrying several organic components with close boiling points, of heat sensitive nature, or tendency in forming azeotropic mixtures. Organic/organic separations by PV can be subdivided into four categories: separation of polar and nonpolar solvents, separation of aromatic and alicyclic mixtures, separation of aromatic, aliphatic, aromatic hydrocarbons, and isomers.
When the energy penalty becomes very high due to the presence of azeotropes or close-boiling point components, pervaporation would be an alternative economical technology to distillation to achieve the desired product quality. The recovery of small quantities of impurities and the enhancement of equilibrium reactions are typical attractive areas for PV.
Petro Sep has developed VOC-SEP™ and AZEO-SEP™ that primarily utilize PV or possibly VP for separation.
Vapor Permeation (VP)
VP, a process similar to pervaporation, is a membrane technique suitable for concentration or efficient separation of valuable compounds, present in the form of saturated vapor in the feed. VP has advantages over PV. PV membranes are in direct contact with the liquid feed. This might cause membrane swelling and increased concentration polarization. In contrast, the VP membrane is in contact with vapor and the membrane stays unaffected, thus enhancing its life. Also, selectivity values are higher in VP but flux is lower compared to PV.
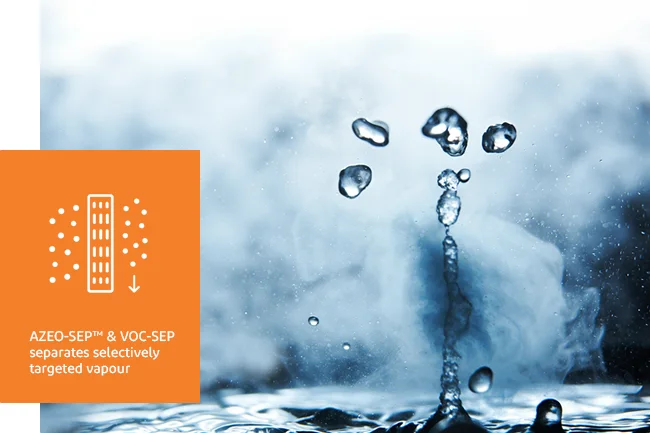
A chemical potential acts as the driving force for the transport of components from the feed to permeate side through creation of a partial pressure difference across the membrane.
VP can be considered advantageous over PV as the membrane in this process, is in contact with a feed in vapor state, thus saving condensation energy and minimizing concentration polarization. The phenomenon of concentration polarization is not seen in VP since vapor permeability is lower and diffusivity value is higher for vapors than liquids. Thus, mass transfer outside the membrane can be neglected since it has a minor influence in separation.
The difference between PV and VP processes is that, the feed in VP is a vapor or a mixture of vapor and gases and permeate obtained is also a vapor, whereas in PV, the feed is a liquid mixture and the permeate is in the form of a vapor, which therefore requires enthalpy of vaporization. In both, VP and PV, the driving force for mass transport across the membrane, is enhanced by maintaining the permeate side under vacuum.
VP involves the same principles and mechanisms of mass transfer and separation as PV, the difference being that the feed fluid is a saturated vapor in VP and a liquid in PV. VP mostly uses nonporous membranes like PV, wherein the mass transport is governed by sorption, diffusion and desorption.
VP is especially advantageous in cases such as purification of top products of fractionating columns where feed is already in the form of a vapor and only the reflux of the column has to be condensed. VP provides higher selectivity than PV, and is also capable of separating low vaporizing enthalpy mixtures such as ethanol-water and methanol-water mixtures, with no phase change occurring during permeation. VP is comparable to gas permeation, wherein the gas mixture consists of permanent gases whereas, in VP, the feed consists of vapors that can be condensed under standard conditions.
Both PV and VP using hydrophilic membranes are popularly being applied in dehydration of various organic solvents. Although the same membrane can be applied for both processes, separation of vaporous mixture of solvents can offer several advantages under certain boundary conditions when compared with pervaporation of liquid feed.
Hybrid distillation processes using either pervaporation or vapor permeation have been found to be a very attractive economic option. Water removal from acetonitrile water mixture using a hybrid distillation-vapor permeation technique was reported to be very effective and economical compared to hybrid distillation-pervaporation.
VP can be easily retrofitted into existing conventional processes owing to lower equipment cost, lesser maintenance requirements, and smaller footprint.
Petro Sep has developed VOC-SEP™ and AZEO-SEP™ that primarily utilize PV or possibly VP for separation.
Petro Sep has pioneered various membrane
technologies from research, engineering to
full scale industrial production
Conventional Filtration (MF/UF/NF/RO)
Pressure driven filtration membrane are classified based on their pore sizes and their suitability for the relevant applications to different categories. These categories are Micro-filters, Ultra-filters, Nano-filters and Reverse Osmosis filters.
Petro Sep as an expert in membrane separation technology for the separation and purification of aqueous and organic mixtures, we provide process engineering services, designs, manufactures and supplies process equipment, as well as turn-key modular plants to the process industry. The main fields of activities comprise:
- Engineering services such as conceptual process design, feasibility studies, plant optimizations including process validation in the test center
- Testing including process development, feasibility and scale-up in a well equipped, state-of-the-art test center
- Specialized process equipment
- Complete separation process plants, in particular modular plants (skids).
Petro Sep as an expert in membrane separation technology for the separation and purification of aqueous and organic mixtures, we provide process engineering services, designs, manufactures and supplies process equipment, as well as turn-key modular plants to the process industry. The main fields of activities comprise:
- Engineering services such as conceptual process design, feasibility studies, plant optimizations including process validation in the test center
- Testing including process development, feasibility and scale-up in a well equipped, state-of-the-art test center
- Specialized process equipment
- Complete separation process plants, in particular modular plants (skids).
Petro Sep as an expert in membrane separation technology for the separation and purification of aqueous and organic mixtures, we provide process engineering services, designs, manufactures and supplies process equipment, as well as turn-key modular plants to the process industry. The main fields of activities comprise:
- Engineering services such as conceptual process design, feasibility studies, plant optimizations including process validation in the test center
- Testing including process development, feasibility and scale-up in a well equipped, state-of-the-art test center
- Specialized process equipment
- Complete separation process plants, in particular modular plants (skids).
Petro Sep as an expert in membrane separation technology for the separation and purification of aqueous and organic mixtures, we provide process engineering services, designs, manufactures and supplies process equipment, as well as turn-key modular plants to the process industry. The main fields of activities comprise:
- Engineering services such as conceptual process design, feasibility studies, plant optimizations including process validation in the test center
- Testing including process development, feasibility and scale-up in a well equipped, state-of-the-art test center
- Specialized process equipment
- Complete separation process plants, in particular modular plants (skids).
Turnkey solutions
that will save you money and help the planet.