Products & Systems
Petro Sep has developed world-leading patented membranes AQUA-SEP®, VOC-SEP® and AZEO-SEP® for the separation of complex fluids.
- We develop innovative proprietary hybrid membrane processes and zero liquid discharge (ZLD) systems. We provide domain expertise in vacuum membrane distillation (VMD), pervaporation (PV) and vapor permeation (VP) for industrial complex fluid separation problems. an that combines.
- Petro Sep membrane systems provide are highly customizable and can be combined and designed for highly selective separation requirements with many advantages:
- High velocity hollow fiber membrane that offers non fouling.
- Highly selective to the target compounds and maximize product quality and purity.
- Low operational energy consumption.
- Modular construction easy to integrated with Existing or New Plants
- Zero liquid discharge Membrane-Based Separation hybrid Systems.
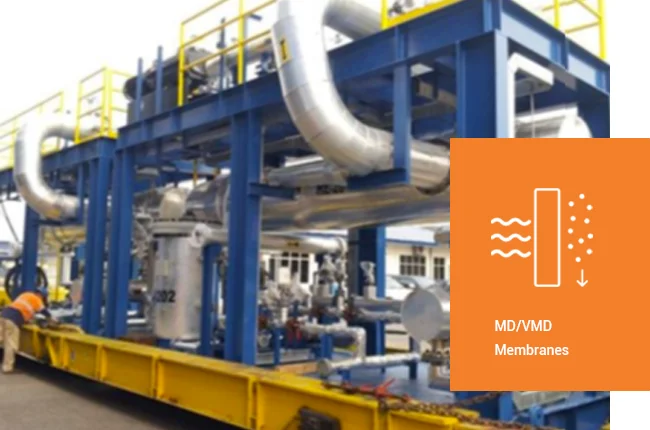
AQUA-SEP®
Aqua-Sep® membranes are utilized in VMD systems to separate water from dissolved solids. Driving force is the differential pressure between the aqueous feed stream and the vapor stream under vacuum, resulting in high flux. The membrane acts as a selective barrier between the feed in the liquid phase and the permeate in the vapor phase.
- Available in both flat sheet and Hollow fiber modules. However, hollow fiber membrane is always preferable due its advantage of elimination the scaling or fouling from membrane surface area.
- Porous membrane increases the flux rate without increasing the concentration polarization on the membrane surfaces.
- Hydrophobic membrane (i.e. it doesn’t let water through), which separates water from an aqueous feed stream. The mass and heat transfer through the membrane is facilitated by an applied vacuum on the permeate side.
- Different membrane construction materials are available for different applications such as Polytetrafluoroethylene (PTFE), Polyvinylidene fluoride (PVDF) and Polyether sulfone (PES)
- Flux rate up to 25 kg/m²h.
- Maximum operating temperature 85˚C.
- Maximum operating pressure 200 kPa.
- Easily integrated in hybrid zero liquid discharge process.
- Economic industrial solution compared with high cost thermally driven separation technologies.
- Lower energy required due to lower operating temperature. While other thermal separation processes require high energy and downtime for scale cleaning.
- Ability to process high TDS feeds (up to 25% salt) compared with the conventional thermal evaporation processes or pressure driven reverse osmosis membrane systems.
- No scaling or fouling due to the hollow fiber membrane module structure. that maintain high velocity inside the tubes of the hollow fiber membrane construction
- High water recovery ratio up to 85%.
- Ability to develop zero liquid discharge hybrid system or alternatively reduce the volume of the disposed concentrated brine stream.
- 50% less energy required per unit of water recovered due to optimized reused of the heat energy.
- Production of biofuel from municipal solid waste processing plant (MSW).
- Purify wastewater from landfill for high quality standard for reuse.
- Treatment of highly concentrated reject stream from thermal seawater desalination plant and Reverse osmosis systems.
- Oil & Gas produced Water.
- Lithium Recovery from mine tailing ponds.
AZEO-SEP® PV/VP Membranes
Azeo-Sep® is utilized in either PV or VP separation processes. In PV, feed stream is in liquid phase, while in VP it in is vapor phase. The driving force of separation is the pressure differential between two sides of the membrane. Generally, membrane material selection and density determine the flux rate and the selectivity of what passes through the membranes. Azeo-Sep® was customized for the dehydration of the process feed stream that forms azeotropic mixtures with water. While thermal distillation fails to achieve efficient dehydration.
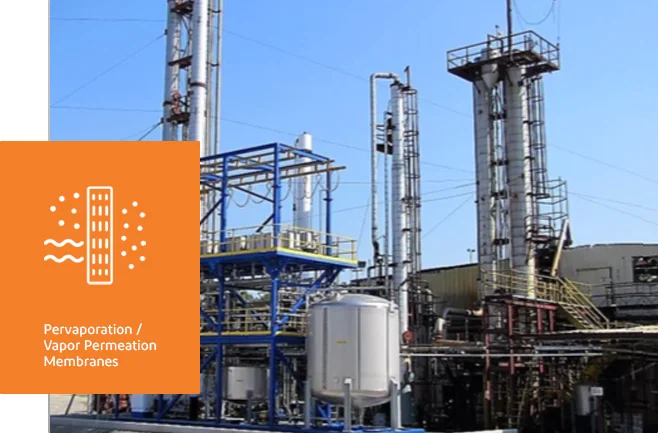
- Available in both flat sheet and Hollow fiber modules. However, hollow fiber membranes are preferred due to easy maintenance, high surface area and low footprint.
- High dense and non-porous membranes to allow high selectivity towards water molecules. However, this high selectivity reduces the flux rate compared with the porous membranes that is used in VMD processes.
- Hydrophilic membrane that selects water to pass through and it excels at breaking down azeotropic mixtures that cannot be distilled through conventional processes.
- Flux rate up to 1 kg/m²h.
- Maximum operating temperature 85˚C.
- Maximum operating pressure 200 kPa.
- Easy to achieve high purity solvents.
- Low-cost PV/VP systems for solvent dehydration compared with high-cost conventional thermal separation processes such as distillation and evaporation.
- Configurable purity levels to meet highest required specifications.
- Ability to achieve high purity of 99.5% in most applications.
- Break all water induced azeotropes.
- Low energy required for the operation of Azeo-Sep® PV/VP systems unlike distillation columns and molecular sieves systems.
- Low to almost no fugitive emissions to air since PV/VP processes runs in closed system.
- Can be integrated in hybrid system with other separation technologies such as VOC-Sep® to provide a complete solution.
- Recycle and purify spent solvents in the paint industry. This solvent is normally disposed as hazardous waste.
- Purifications and recovery of a wide range of industrial solvents.
- Separation of water from organics mixtures.
- Dehydration of ethanol produced during the fermentation of sugar extracted from municipal solid waste (MSW) for industrial use or as ingredient in biofuel.
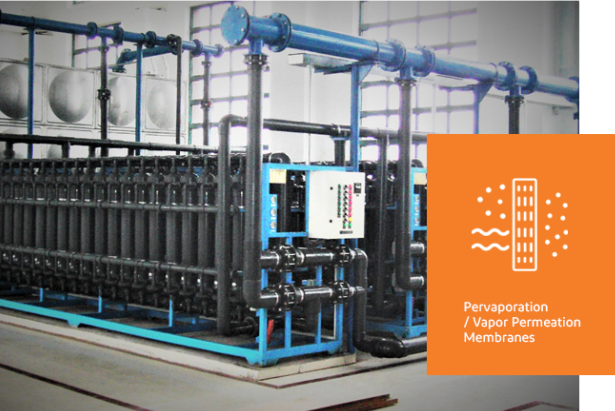
VOC-SEP® PV/VP Membranes
VOC-Sep® is utilized in in either PV or VP separation processes. In PV, feed stream is in liquid phase, while in VP it in is vapor phase. The driving force of separation is the pressure differential between two sides of the membrane. VOC-Sep® PV/VP systems selectively allow Volatile Organic Compounds (VOC’s) to diffuse through the membrane but not water due its hydrophobicity. It can also be customized to eliminate organic pollutants from aqueous streams and separation of organic-organic mixtures
- Available in both flat sheet and Hollow fiber modules. However, hollow fiber membranes are preferred due to easy maintenance, high surface area and low footprint.
- High dense and non-porous membranes allow high selectivity towards VOCs molecules.
- Hydrophobic membrane separates volatile organic compounds (VOCs) from water.
- Flux rate up to 1 kg/m²h.
- Maximum operating temperature 70˚C.
- Maximum operating pressure 200 kPa.
- Separation of organic-organic mixtures and water-organic mixtures.
- Recovery of VOCs from water mixtures when they are low in concentration. Such mixtures are regularly disposed as hazardous industrial wastewater.
- VOC-Sep® VP process can be utilized as standalone system to produce product that has very good quality to make it reusable.
- In combination with Azeo-Sep®, VOC-Sep® can achieve very efficient selective separation and high purity product quality.
- Low energy required for the operation of VOC-Sep® PV/VP systems and can utilize existing waste heat, if available, unlike distillation columns and thermal evaporation processes.
- Low to almost no fugitive emissions to air since PV/VP processes runs in closed system.
- Separation of volatile organic compounds from water mixtures such as ethanol-water and methanol-water mixtures.
- Purification of top products of fractionating columns where feed is already in the form of a vapor and only the reflux of the column has to be condensed.
- Separation of ethanol produced in the fermentation process of the extracted sugar from the municipal solid waste MSW. This produced ethanol is used in biofuel.
- Recovery of light hydrocarbons from the produced water tailing ponds in oilfields.
Conventional Membranes
Depending on the feed specifications and separation needs, Petro Sep complements and supplies products that integrate with conventional industrial processes as necessary as well as standard membrane filtrations.
Petro Sep’s industrial water filtration membranes are porous membranes, where the separation is determined by the pore size of the membrane and the particle size of the supplied feed.
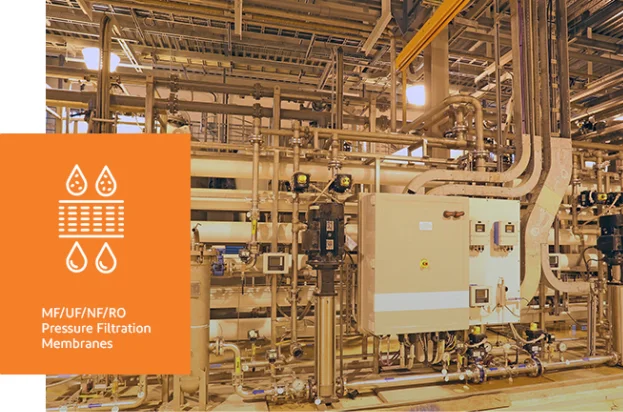
- Petro-SEP® Microfiltration (MF)
- Petro-SEP® Ultrafiltration (UF)
- Petro-SEP® Nanofiltration (NF)
- Petro-SEP® Reverse-Osmosis (RO)
YEARS OF
EXPERIENCE
1999
Est. Year
Petro Sep Started as a Membrane Research & Development Company
50+ Yrs.
Core Membrane-Technology Experience
Petro Sep has pioneered world- leading membrane systems
100+
Projects Delivered Globally
Petro Sep has pioneered world- leading membrane systems
Petro Sep has pioneered various membrane
technologies from research, engineering to
full scale industrial production
Petro Sep as an expert in membrane separation technology for the separation and purification of aqueous and organic mixtures, we provide process engineering services, designs, manufactures and supplies process equipment, as well as turn-key modular plants to the process industry. The main fields of activities comprise:
- Engineering services such as conceptual process design, feasibility studies, plant optimizations including process validation in the test center
- Testing including process development, feasibility and scale-up in a well equipped, state-of-the-art test center
- Specialized process equipment
- Complete separation process plants, in particular modular plants (skids).
- Zero-Liquid Discharge (ZLD) is a treatment process that allows recovery of water or desired solvents and dehydrating the remaining constituents in a solid form. As such, only high-purity water or solvent remain, and no liquid waste is produced.
- Industrial and chemical processes heavily rely on water and solvents. However, most of the waste produced, including the liquid waste, is dumped in either landfills or waterbodies. Some of the waste cannot be recycled by conventional methods and some waste is partly recycled or reused, even when the waste contains valuable constituents that could be reused.
- Petro Sep has pioneered innovative membrane-based systems that can be customized to treat, process and separate liquid waste streams resulting in zero liquid waste (zero liquid discharge or ZLD). Petro Sep’s existing products, such as AQUA-SEP™, VOC-SEP™ or AZEO-SEP™ can easily recover water with up to 99.99% purity (ultrapure water) from various streams and even separate mixtures that cannot be separated through conventional distillation, such azeotropic mixtures of ethanol recovery.
- For example, a conventional wastewater recovery reverse-osmosis (WWRO) plant generally provides up to 75-85% efficiency in water reclamation and contaminant removal. Petro Sep membrane systems that can further treat water and recover valuable compounds and chemicals and recover high-purity water and solvents with zero-liquid discharge (ZLD).
- Similarly, a desalination RO plant may remove 60-75% of the salts and return the remaining retentate, a highly concentrated brine, back to the water source. Over time, the returned brine is likely going to affect the salinity of the source feed and will further compromise RO plant efficiencies.
- Petro Sep membranes resist salt damage and can further treat the reject brine from desalination plants upwards of 99.99% purity at lower temperatures than conventional distillation methods and produce a zero-liquid discharge.
- There are numerous other applications where Petro Sep solutions can entirely recover the source solvents out of the wastewater and thus providing a multifold economic and environmental benefit for existing operations requiring a ZLD treatment.
Turnkey solutions
that will save you money and help the planet.